当社のノズル加工におけるコストダウン事例をご紹介
吸着ノズルや塗布ノズルなど、世の中のすべてのノズルは、何らかの影響により消耗するものです。工業的に使用するノズルであれば、より長持ちさせランニングコストを抑えるよう消耗の原因を掴み、対策を行うことが求められます。
一般にノズルは、下記の要因により消耗したり、破損したり、使えなくなってしまいます。
①摩耗・変形
②詰まり
消耗品でもあるノズル製品は購買頻度が高いために、お客様は出来る限り価格を抑えて購入したいとご要望をよくいただきます。そこで今回のコラムでは、過去に当社にお寄せいただいたご要望の中から、実際に当社が対応したコストダウン事例をご紹介します。
>>技術コラム【ノズルを長持ちさせるには?】はこちら
要望① 吸着ノズルに長くて細い楕円穴を開けて欲しい
お客様の要望として、既存ノズルに細長い楕円穴を開けて欲しいとのことでした。一般的には楕円形状に合わせて細穴加工を行い、その後にワイヤーカット加工を行います。しかし当社の場合は細穴加工のみ加工をします。これにより段取り替えの時間を短縮することが可能となり、コストダウンにつながります。
要望② 穴詰まりを無くしたい
穴詰まりでお悩みのお客様は多くいらっしゃいます。液体の通る内面の面粗度が悪い場合は、表面に少しずつ液体が付着し、最終的には穴が詰まる場合があります。こうしたことを回避するために、ノズル内面は極力なめらかに仕上げることが求められます。そのため当社ではテーパー部分をラップ研磨で梨地状に仕上げることにより、内部での滞留を抑制しています。液の滞留が少なくなると、ノズルの一部分にのみかかる圧力が無くなり、ノズル寿命の延命化につながります。
要望③ とりあえず長持ちさせたい
ノズルは使用頻度に比例して、吸着対象物との接触面がすり減ってきたり、変形したりします。さらに、吐出する液体が通過するときに少しずつ穴の内面が摩耗し、穴径が大きくなることにより、吐出量が変化し、通常の使用が不可能になることもあります。そのため長持ちを最優先と考えるお客様に対して、オール超硬を採用しています。コストダウンの観点から根元だけステンレスを採用する場合もあります。しかし全体的なコストパフォーマンスを考慮するとオール超硬の方が優位です。
当社のノズル製作事例を一部ご紹介
超硬吸着ノズル(先端0.8×0.8四角錐形状)
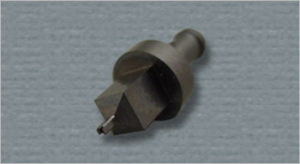
超硬製 角錐コレット
この超硬製の角錐コレットは、当社の設備にてオール超硬で製作したものです。まず研削で外形加工を行った後、φ0.6穴部とφ0.2吸着面の穴部を細穴放電加工機にて加工しました。さらに吸着面の角錐部は型彫放電加工機にて、120°の角度で四角錐形状に加工を行っています(上記写真の右上の拡大図をご覧ください)。
また、この角錐コレットは小さなチップ部品を搬送するために使われるため、チップ部品を確実に吸着できるように角錐部に鏡面ラップ仕上げを施しています。
この小さな角錐コレットを製作するためには、研削・細穴放電加工・型彫放電加工・鏡面ラップ仕上げと多岐にわたる工程を経ることが必要な上、それぞれの工程で高い技術力が要求されます。特注精密ノズル加工.COMを運営する㈱キンコーでは、超硬に対する微細・高精度な加工でも、加工ノウハウと各種加工機をフル活用することでお客様の加工ニーズにお応えいたします。超硬製のコレットやノズルでお困りなら、当社にお任せください。
当社に過去寄せられたノズルに関するご質問を一部ご紹介
>>『ノズルの内面テーパー角度を厳しく絞りたいですが、可能ですか?』はこちら
>>『使用ノズルの噴射に上手く広がらないので相談に乗ってもらえますか?』はこちら